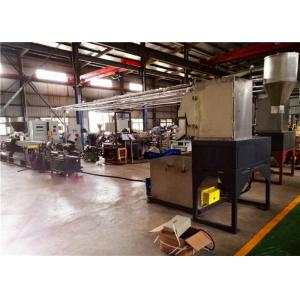
Add to Cart
65mm Hight Torque Twin Screw Extruder with Uner Water Pelletizer for Thermoplastic
No. | Denomination of the delivery | |||||||||||||||||||||||||||||||||||||||||||||||||||||||||||||||
1.0 | Metering system | |||||||||||||||||||||||||||||||||||||||||||||||||||||||||||||||
1.1 | Silo and up loader for PP | |||||||||||||||||||||||||||||||||||||||||||||||||||||||||||||||
Silo Vol.: 0.5m3; Material: stainless steel; With alarm for material level; Auto up-loader: 1 set capacity: 0-200kg/hr; | ||||||||||||||||||||||||||||||||||||||||||||||||||||||||||||||||
1.2 | Loss-in-weight feeder for PP | |||||||||||||||||||||||||||||||||||||||||||||||||||||||||||||||
K-tron loss-in-weight feeder Capacity: 20-200 kg/hr; Feeding method: by twin screws; Flow controlling: PLC; RPM controller: AC inverter; Main components: Weighting transducer and terminal: Metro Toledo; Controlling terminal: controller; | ||||||||||||||||||||||||||||||||||||||||||||||||||||||||||||||||
1.3 | Silo and up-loader for EPDM | |||||||||||||||||||||||||||||||||||||||||||||||||||||||||||||||
Silo Vol.: 0.5m3; Material: stainless steel; With alarm for material level; Auto up-loader: 1 set capacity: 0-200kg/hr; | ||||||||||||||||||||||||||||||||||||||||||||||||||||||||||||||||
1.4 | Loss-in-weight feeder for EPDM | |||||||||||||||||||||||||||||||||||||||||||||||||||||||||||||||
K-tron loss-in-weight feeder Capacity: 20-200 kg/hr; Feeding method: by twin screws; Flow controlling: PLC; RPM controller: AC inverter; Main components: Weighting transducer and terminal: Metro Toledo; Controlling terminal: controller; | ||||||||||||||||||||||||||||||||||||||||||||||||||||||||||||||||
1.5 | Loss-in-weight feeder for liquid | |||||||||||||||||||||||||||||||||||||||||||||||||||||||||||||||
K-tron Loss-in-weight feeder Capacity: 5-50L/hr; Flow controlling: PLC; RPM controller: AC inverter; Main components: Weighting transducer and terminal: Metro Toledo; Controlling terminal: controller; | ||||||||||||||||||||||||||||||||||||||||||||||||||||||||||||||||
1.6 | Feeding hopper | |||||||||||||||||||||||||||||||||||||||||||||||||||||||||||||||
200L Stainless steel made | ||||||||||||||||||||||||||||||||||||||||||||||||||||||||||||||||
1.7 | Support frame | |||||||||||||||||||||||||||||||||||||||||||||||||||||||||||||||
One support frame for main feeding system One for liquid feeding system | ||||||||||||||||||||||||||||||||||||||||||||||||||||||||||||||||
2.0 | CHT65D compounding unit | |||||||||||||||||||||||||||||||||||||||||||||||||||||||||||||||
2.1 | CHT65D co-rotating twin screw extruder | |||||||||||||||||||||||||||||||||||||||||||||||||||||||||||||||
Main motor: AC motor,132KW; SCHENEIDER regulator WITH GLOBAL GUARANTEE Motor rotation speed:1500rpm/600rpm Power transmission: The transmission system applied the torque over load protector which is designed by our company. It can prevent the damage to the driving element when it is started or over loaded.
Gearbox: High safety factor design; Latest steel alloy material for gears applied with special heat treatment and manufactured at high precision level; NSK bearings and imported seals applied, Special lubricating system equipped combined with immersing and forcing solutions; Input/output rotary speed:1500/600rpm; Torque:2x1050N.M Torque degree: 9.2T/A3 Oil pump motor power:1.1kw
Extrusion line: Screw Diameter: 64mm,L/D:52:1; Maximum Screw speed:600rpm; Screw configuration:with modular structure, torque transmission by spline; Screw material: High speed tool steel W6Mo5Cr4V2,HRC58-62; Barrel configuration: with modular structure, each one with length of 4L/D,and the barrels connected together by bolts and pins; Barrel material: 45# steel, The inner surface of the linear isα301,surface hardness is HRC62-65;
Recommended barrels configuration:
No1 barrel with one feeding port for all possible components,, No.3 and No5 with one liquid feeding port, No.9 is a venting port. That is blocked with one plug if necessary. No 10 preserve one liquid injection port. No12 with vacuum port Temperature controlling: Heating system: electric heater, total heating power with approx.55 kw (No.1 Section cooled by water);The solenoid valves are ACL from Italy Cooling system:soft-water cooling system; Temp. controller:PID; Soft-water cooling system including one 1.5kw water-pump, stainless steel water-box (with water Temp. gauge), heat exchanger, imported solenoid valves, water pressure indicator etc.
Steel base: Welding base with special pads; | ||||||||||||||||||||||||||||||||||||||||||||||||||||||||||||||||
2.2 | Vacuum system | |||||||||||||||||||||||||||||||||||||||||||||||||||||||||||||||
Vacuum Pump Mode: Water Ring Vacuum Pump Material Baffle Plate:40Cr; Vacuum Pump Power:5.5kw; Vacuum Degree:-0.95MPa With Vacuum Gauge and dual Filtering Pot | ||||||||||||||||||||||||||||||||||||||||||||||||||||||||||||||||
2.3 | Hydraulic screen changer | |||||||||||||||||||||||||||||||||||||||||||||||||||||||||||||||
Structure Mode: Plate type Driving Mode:Hydraulic Action Time: <1S; Driving Mode: Hydraulic Station The hydraulic station includes: Driving Oil Pump1.5kw, Highest pressure20Mpa, with safety valve, accumulator. The inspection on pressure and temperature: Set one inspection position before the screen and display the melt temperature. Heating power:4kw, cast-Al heater Accumulator6.3L Filtering area:6400 mm^2 | ||||||||||||||||||||||||||||||||||||||||||||||||||||||||||||||||
3.0 | Under water pelletizing system | |||||||||||||||||||||||||||||||||||||||||||||||||||||||||||||||
3.1 | Diverter valve | |||||||||||||||||||||||||||||||||||||||||||||||||||||||||||||||
Hydraulic station driving; 38CrMoAlA made with nitrification treatment; | ||||||||||||||||||||||||||||||||||||||||||||||||||||||||||||||||
3.2 | Under water pelletizer | |||||||||||||||||||||||||||||||||||||||||||||||||||||||||||||||
Motor power 5.5 kw with rated speed 2900rpm; Material of cutting knives: high speed tool alloy with vacuum quenching heat treatment; S.S. for cutting hub; Mechanical forcing principle for cutting head to die plate; NSK bearings equipped; | ||||||||||||||||||||||||||||||||||||||||||||||||||||||||||||||||
3.3 | Water circulating system | |||||||||||||||||||||||||||||||||||||||||||||||||||||||||||||||
Water pump: 4kw S.S made water tank Including heating and temperature controlling system Including by-pass pipe line | ||||||||||||||||||||||||||||||||||||||||||||||||||||||||||||||||
3.4 | Centrifugal dryer | |||||||||||||||||||||||||||||||||||||||||||||||||||||||||||||||
Driving Power:4kw, Diameter of Centrifugal Conister:500mm, Diameter of Sieve Hole:0.5-1mm, Material:Stainless Steel, There is a pre filtering device at the entrance | ||||||||||||||||||||||||||||||||||||||||||||||||||||||||||||||||
3.5 | Vibrator | |||||||||||||||||||||||||||||||||||||||||||||||||||||||||||||||
Motor Power: 2x0.2kw Capacity:100-400kg/hr Discharging Gap: 3, qualified pellets, huge pellets, small pellets Made of stainless steel | ||||||||||||||||||||||||||||||||||||||||||||||||||||||||||||||||
3.6 | Conveyer and silo | |||||||||||||||||||||||||||||||||||||||||||||||||||||||||||||||
Conveying part: Motor power for fan: 3kw Pipe material: stainless steel Conveying capacity: more than 800kg/hr Silo part: Silo volume:1000L Material: stainless steel Disassembly supporter | ||||||||||||||||||||||||||||||||||||||||||||||||||||||||||||||||
4.0 | Control cabinet | |||||||||||||||||||||||||||||||||||||||||||||||||||||||||||||||
4.1 | Cabinet for Loss-in-feeders | |||||||||||||||||||||||||||||||||||||||||||||||||||||||||||||||
Schneider inverter Low voltage components: Schneider Schneider PLC and touch screen equipped | ||||||||||||||||||||||||||||||||||||||||||||||||||||||||||||||||
4.2 | Cabinet for extrusion line | |||||||||||||||||||||||||||||||||||||||||||||||||||||||||||||||
4.2.1. The temperature controlling system applies RKC from Japan 4.2.2. The current of main extruder: RKC displayer. Interlocked with the main extruder to avoid over current 4.2.4. Main Extruder Interlock Protection Function: a,Main Extruder interlocks with the lubricant pump for the gear box and the fan for the main motor b,Main extruder interlocks with the feeder, when the extruder stops, the feeder will stop immediately; c,The main motor has protective functions of over current, under voltage, lack of phases, over heat and block running. D,There is melt pressure and melt temperature display function on the die, of which the melt pressure interlock with the main extruder to realize the over pressure protection on the die 4.2.3.Low voltage element: SCHNEIDER with global guarantee 4.2.4.Speed regulator for main extruder: SCHNEIDER with global guarantee | ||||||||||||||||||||||||||||||||||||||||||||||||||||||||||||||||
4.3 | Controlling system for under water pelletizing system | |||||||||||||||||||||||||||||||||||||||||||||||||||||||||||||||
All electric system is installed in a separate cabinet Siemens PLC controller with touch screen programming Manual or automatic control model |